The Hidden Costs of Traditional Compliance Training in Manufacturing: Time, Money, and Output
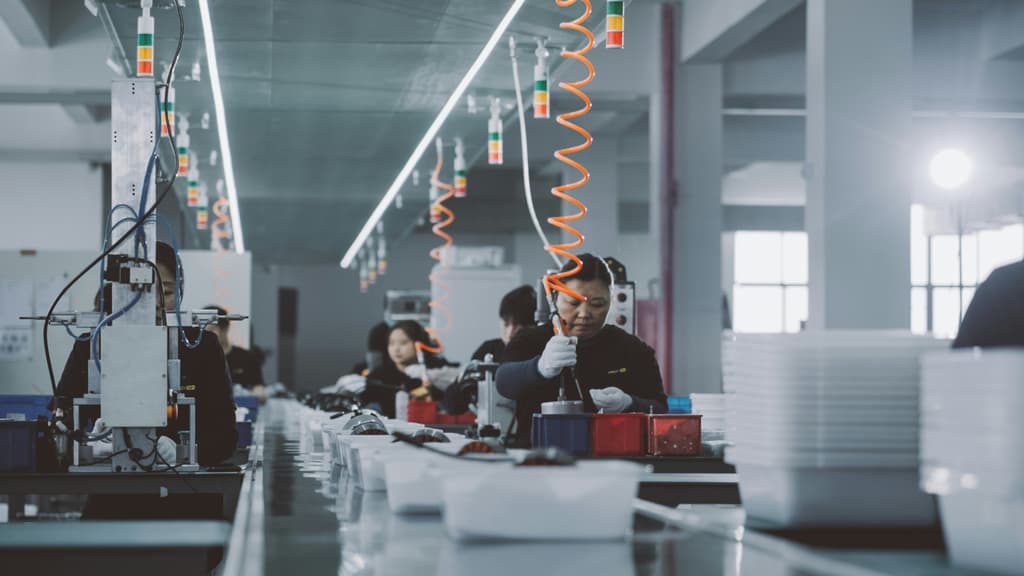
Main Takeaways
- Traditional compliance training methods in manufacturing, such as in-person sessions and off-site seminars, come with significant hidden costs like time lost, financial burdens, and reduced overall output, which often go unnoticed.
- Traditional training disrupts workflows by pulling employees away from their stations, causing delays in production and reducing overall operational efficiency.
- The expenses tied to traditional training—such as hiring trainers, travel, materials, and lost work hours—quickly add up, straining the company's budget.
- Adopting digital compliance training solutions can save time, cut costs, improve knowledge retention, and enhance productivity, all while minimizing disruption to regular operations.
- Digital compliance platforms provide measurable insights through tracking and analytics, helping organizations assess and optimize training effectiveness for better long-term results.
In the fast-paced world of manufacturing, compliance training is a necessary but often overlooked aspect of operations. While essential for maintaining safety standards and regulatory adherence, traditional compliance training methods can harbor significant hidden costs that impact your bottom line.
The Current State of Compliance Training in Manufacturing
Manufacturing companies face a complex web of regulations, from OSHA standards to industry-specific requirements. Traditionally, compliance training has involved in-person sessions, bulky manuals, and off-site seminars. While these methods have been the norm, they come with a host of challenges that many manufacturers fail to fully recognize.
Hidden Costs of Traditional Compliance Training
Time
One of the most significant hidden costs of traditional compliance training is time. Consider the following:
- Lengthy training sessions that pull employees away from their work for hours or even days
- Travel time for off-site training, which can be substantial for multi-location operations
- Scheduling conflicts that disrupt production flows
- Lost work hours that directly translate to reduced output
These time-related costs can accumulate quickly, leading to substantial productivity losses that may not be immediately apparent on financial statements.
Financial Burden
The financial impact of traditional compliance training extends far beyond the visible expenses:
- Direct costs include hiring trainers, purchasing materials, and renting venues
- Indirect costs encompass employee wages during training periods
- Opportunity costs arise from halted production lines
- Potential fines for non-compliance if training is inadequate or outdated
Impact on Output and Quality
Traditional training methods can have a ripple effect on your manufacturing output and product quality, leading to costly mistakes, recalls, or customer dissatisfaction.
- Decreased production during training periods as employees are away from their stations
- Potential for errors due to information overload in intensive, infrequent training sessions
- Quality issues arising from inadequate retention of training material
Benefits of Modern Compliance Training Solutions
Modern training solutions, such as e-learning platforms and micro-learning modules, offer a more efficient alternative to traditional methods. These approaches come with several key advantages:
- Flexibility: Employees can access training on-demand, minimizing interruptions to their workflows. This flexibility ensures that compliance training doesn’t disrupt production schedules.
- Cost-Effectiveness: With a flat-rate pricing model, organizations can save money compared to traditional training methods, which often involve multiple direct and indirect costs.
- Engagement: Interactive content and modern training formats improve knowledge retention and employee engagement, leading to better outcomes in compliance and productivity.
Did you know?
Platforms like EasyLlama offer a modern approach to compliance training in manufacturing, that can address many of the hidden costs associated with traditional training methods:
- On-demand, mobile-friendly learning modules
- Customizable content that addresses specific manufacturing needs
- Real-time tracking and reporting for easy compliance management
Measuring the ROI of Digital Compliance Training
The benefits of transitioning to digital compliance training are tangible and measurable:
Time Savings
Digital compliance training significantly reduces time investment compared to traditional methods. Employees can access training on-demand during downtime, complete modules at their own pace, and engage in microlearning sessions that fit into busy schedules. The elimination of travel time for off-site training saves substantial hours, allowing workers to remain productive. This flexible approach minimizes disruptions to regular work while ensuring compliance requirements are met efficiently.
Cost Reductions
By eliminating travel expenses for off-site training and reducing the need for physical materials, companies can substantially lower their training-related expenditures. The ability to reuse digital content across multiple sessions reduces instructor fees, while the decreased time employees spend away from their primary tasks minimizes productivity losses. These combined savings make digital compliance training a cost-effective solution for organizations looking to optimize their training budgets without compromising on quality or effectiveness.
Improved Retention
Incorporating interactive content helps learners to engage more actively with the material, leading to better understanding and recall. Spaced repetition techniques, built into digital platforms, reinforce key concepts over time, enhancing long-term memory. Multimedia elements such as videos and simulations cater to diverse learning styles, making the content more accessible and memorable. Additionally, immediate feedback and assessments help solidify understanding by allowing learners to quickly identify and correct misconceptions, resulting in more effective and lasting compliance knowledge.
Enhanced Productivity
Digital compliance training significantly boosts productivity in manufacturing. Flexible scheduling allows training during natural production lulls, minimizing disruptions. Mobile accessibility enables employees to complete training during commutes or off-hours, maximizing efficiency. Automated tracking reduces the administrative burden on HR and management, while readily available materials facilitate faster onboarding of new employees. These factors collectively create a more streamlined workforce, enhancing productivity while ensuring compliance standards are met.
Measurable Outcomes
On top of that, digital compliance training platforms offer valuable analytics to assess overall training effectiveness. Organizations can track completion rates and time spent on modules, gaining insights into engagement. Assessment scores provide immediate feedback on knowledge acquisition, while post-training surveys monitor behavioral changes. Comparing compliance violation rates before and after training offers clear evidence of its impact, enabling continuous optimization of programs for maximum ROI and improved compliance outcomes.
Embracing the Future of Compliance Training
The hidden costs of traditional compliance training in manufacturing can be significant and affect various aspects of your operations, from time and money to productivity and employee morale. By recognizing these overlooked expenses and switching to innovative digital solutions like EasyLlama, manufacturers can make a real difference. This change not only helps cut costs but also boosts efficiency, enhances product quality, and increases employee satisfaction. In today's competitive manufacturing landscape, modernizing your compliance training is essential for staying ahead.
FAQs
-
What are the main hidden costs of traditional compliance training? Time, financial burdens, and reduced output are the primary hidden costs associated with traditional compliance training in manufacturing.
-
How does traditional compliance training impact productivity? Employees spend significant time away from their duties, which decreases overall productivity and disrupts workflows.
-
What are the benefits of switching to digital compliance training? Digital training offers time flexibility, cost savings, improved knowledge retention, and better productivity without disrupting operations.
-
How can digital training improve compliance in manufacturing? By providing on-demand, accessible training, companies ensure continuous learning, better engagement, and measurable outcomes, ultimately improving compliance rates.
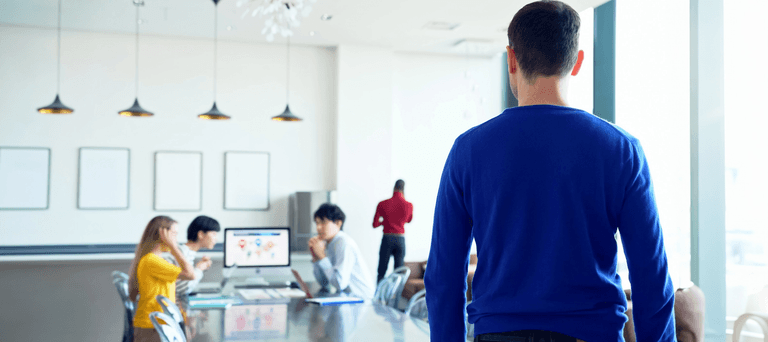
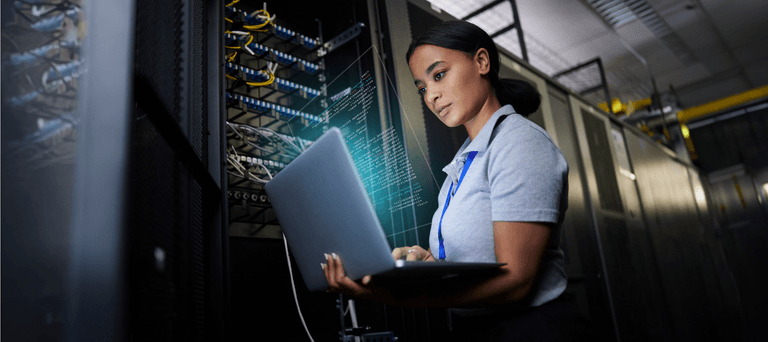
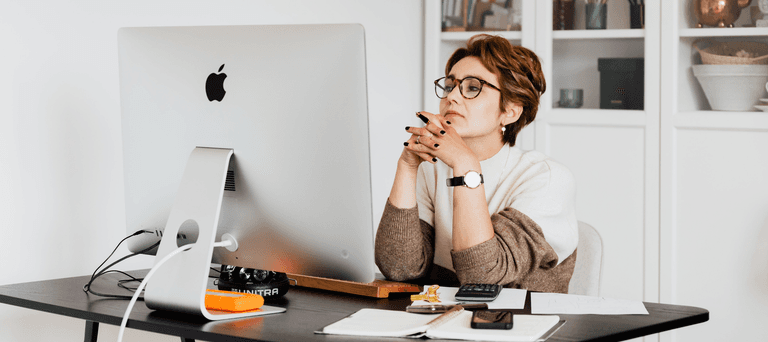
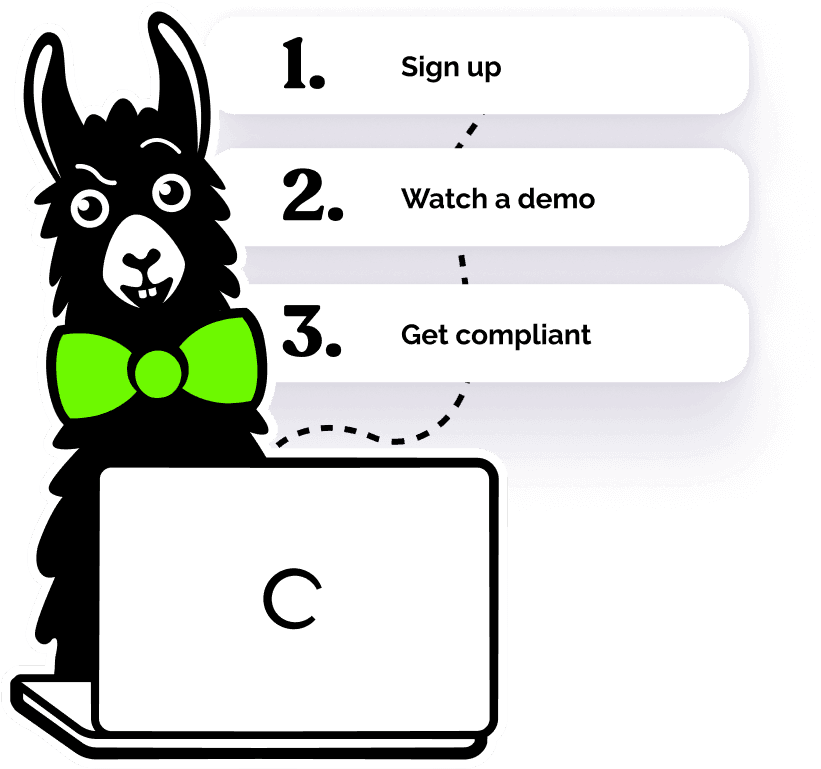
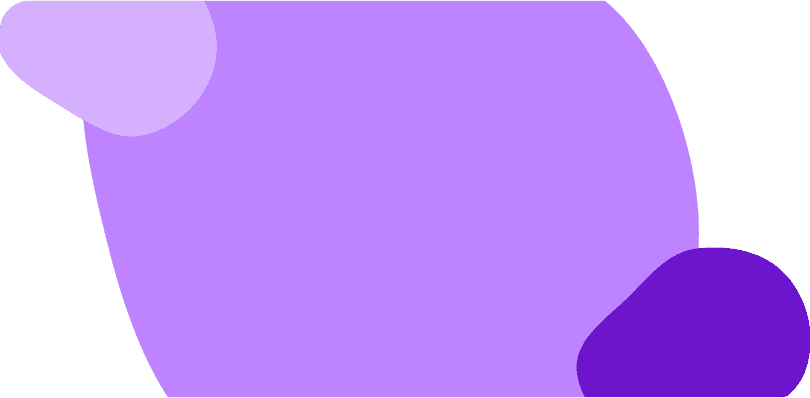